The principle of phase equilibrium of high alumina refractory bricks
2018-04-03
When the temperature of the high alumina refractory brick is above 1545°C, the amount of solid phase (mullite or corundum) increases as the content of A12O3 increases, and the amount of liquid phase that can be generated in the product decreases accordingly. As the phases in the product phase change, the fire-resistance of the product changes. This is due to the high fire-resistant properties of the crystalline mullite or corundum. However, when there is a small amount of flux impurities, the fire resistance of the product is severely reduced. Because the amount of liquid phase increases, the temperature of liquid phase formation also decreases. From this, it can be seen that the raw material for producing high-alumina firebrick must be pure, otherwise, even if the content of A12O3 in the product is increased, good results are not obtained.
When the content of A12O3 in the high alumina refractory brick is less than 72%, the only stable solid phase is mullite before the highest temperature (1870°C). In addition to the amount of SiO2 in the mullite composition, the remaining SiO2 and the fluxing agent form a glassy state, which is converted into a liquid phase at high temperatures. Within this range, the liquid phase forms at 1545°C. In fact, due to the flux material, the temperature of the liquid phase is also lower. When the composition of the product is close to the mullite phase (71.8% A12O3, 13.2% SiO2), the formation of the liquid phase is reduced and the fire resistance of the product is also improved. Therefore, high alumina refractory bricks with less than 72% A12O3 content have improved fire resistance with increasing mullite content.
For products with a content of Al2O3 greater than 72%, the temperature of the liquid brush in the absence of flux is 1850°C in the mullite-corundum system. In fact, due to the flux material (usually about 1-3%) contained in the raw material, the liquid-phase formation temperature is reduced to 1600-1700°C. At the same time, the load softening starting point of the product decreases. Obviously it is much higher than high alumina refractory products with less than 72% Al2O3 content.
The thermal stability of high-alumina refractory bricks depends not only on the grain size of the product. At the same time, due to the different Al2O3 content, the phase composition in the product also affects this property. In products with less than 72% Al2O3 content, the mullite crystal phase increases with the increase of Al2O3, and its thermal stability also increases. When the content of Al2O3 is more than 72%, the existing crystal phases are mullite and corundum, and the change in thermal stability at this time is another case. Increasing the content of Al2O3 will increase the number of just kings. The corundum has a larger thermal expansion coefficient than mullite (corundum linear expansion rate is 0.8-0.85% at 1000°C; mullite is 0.50-0.557 right), which promotes lower thermal stability. At the same time, increasing the corundum content will increase the strength and thermal conductivity of the product and also increase the index of thermal stability.
In high-alumina refractory bricks, increasing the content of Al2O3 enhances the resistance of the product to alkaline slag, particularly to acidic slag. This is because the amount of Al2O3 in the high-alumina firebrick increases, the content of liquid phase decreases, the amount of mullite increases (Al2O3 content is more than 72%), and the amount of corundum phase also increases (Al2O3 content More than 72%). For pure corundum products (98-99% Al2O3), it has the highest slag resistance. This is due to the fact that the inertness of corundum is greater than that of mullite. However, the resistance of high-alumina refractories to alkaline slag is inferior to that of magnesium bricks, magnesium chrome bricks, magnesium spinel bricks, dolomite bricks and other basic refractory materials. This is related to the acidic nature of Al2O3.
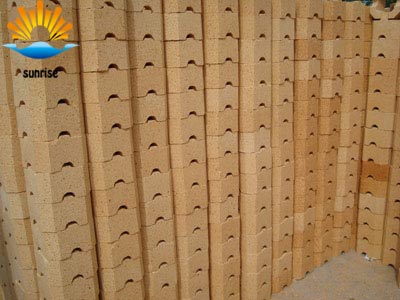