Performance and Application of Low Thermal Conductivity Multi-layer Composite Mullite Brick
2018-04-26
At present, large and medium-sized cement rotary kiln in China generally use silicon molybdenum bricks as the preferred refractories for non-firing belts. However, as molybdenum bricks are used as the main raw materials, corundum phase is the main phase and high-aluminum natural bauxite clinker is used. The addition of more silicon carbide leads to a larger thermal conductivity, the surface temperature of the rotary kiln shell is high, and the heat loss is large, which increases the burning heat loss of the clinker, and the use effect is not ideal.
The low thermal conductivity multi-layer composite mullite brick (Fig. 1) adopts a multi-layer composite structure with working layer, thermal insulation layer and thermal insulation layer. The use of alumina-based sintered mullite instead of the traditional bauxite clinker used as the main raw material, mullite as the main phase, to reduce the overall thermal conductivity of the mullite brick, high-temperature structural strength is effective improve. Based on the poor erosion resistance of mullite-reducing slag, by adding some compound additives and increasing the matrix alumina content to optimize the matrix, the alkali corrosion resistance of refractory bricks is improved. In order to further reduce the thermal conductivity of the working layer of the product, 97# silicon carbide fine powder with good crystal development is used, and andalusite fine powder is added to reinforce the matrix, which reduces the thermal conductivity and improves the high temperature structural strength of the firebrick. Thermal shock stability.
(1) Working layer: Using M70 alumina-based sintered mullite as the main raw material, homogenized bauxite as aggregate and powder, and adding andalusite, carbonized cinnamon and other multiple additives to extend the service life. The performance index of the working layer is: Al2O3 ≥ 67%, apparent porosity is ≤ 20%, bulk density is 2.70 g/cm3, cold pressure strength is 90 ~ 100 MPa, load softening temperature is more than 1650°C, thermal shock stability (1100°C water cooling) ≥ 30 times, the overall thermal conductivity is ≤ 1.65 W/(m·K).
(2) Insulation layer: mainly based on mullite, using M60 clay-based sintered mullite as the main raw material, adding some compound additives to adjust the expansion coefficient, making it close to the working layer, avoiding the connection from sintering or use Cracks occur. Under the premise of satisfying strength, heat insulation effect is improved.
(3) Insulation: Thermal conductivity is a measure of the thermal conductivity of a substance. The thermal conductivity of different materials varies greatly. By adding a material with a lower thermal conductivity in the heat-insulating layer, the overall thermal conductivity is reduced. In the premise of satisfying the strength, the thermal insulation effect of the fire brick is improved.
In the area where the product is used on a rotary kiln, the barrel temperature can be reduced by 50~80°C. The average temperature of the transition zone before the rotary kiln is 250°C, and the heat insulation effect is obvious. It is especially suitable for the front transition zone of large and medium cement rotary kiln. The service life is not less than spinel brick, silicon molybdenum brick or silicon molybdenum brick. In addition to the application of the transition zone before the rotary kiln, the use of the third air duct, grate cooler side wall, etc., will also achieve satisfactory results.
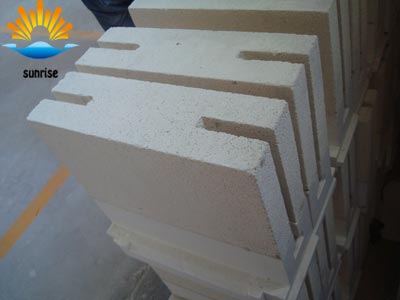