The composition and application of silica brick
2019-09-03
Silica bricks are acidic refractories composed of tridymite, cristobalite, and a small amount of residual quartz and glass phases. The silica content is 94% or more. The true density is 2.35g/cm3. With acid slag corrosion resistance. Higher high temperature strength. The load softening start temperature is 1620 to 1670 °C. Long-term use at high temperatures does not deform. The thermal shock stability is low (heat exchange in water for 1~4 times), natural silica is used as raw material, and an appropriate amount of mineralizer is added to promote the conversion of quartz in the green body into scaly quartz under the reducing atmosphere of 1350~1430 °C. Slowly burned. When heated to 1450 ° C, there is about 1.5~2.2% of total volume expansion. This residual expansion will make the joints tight and ensure the good air tightness and structural strength of the masonry.
The mineral phase composition of silica bricks is mainly tridymite and cristobalite, as well as a small amount of quartz and vitreous. Quartz, cristobalite and residual quartz change greatly in volume at low temperatures, so the thermal stability of silica bricks at low temperatures is very poor. During use, it should be slowly heated and cooled below 800 °C. Otherwise, cracks are likely to occur, so it is not suitable for use in furnaces with rapid temperature changes below 800 °C.
The properties and processes of silica bricks are closely related to the crystal transformation of SiO2. Therefore, true specific gravity is an important quality indicator for silica bricks. The general requirement is below 2.38, and the high quality silica brick should be below 2.35. The true specific gravity is small, reflecting that the number of quartz and cristobalite in the brick is large, and the amount of residual quartz is small, so that the residual line is small in expansion and the intensity in use is also reduced.
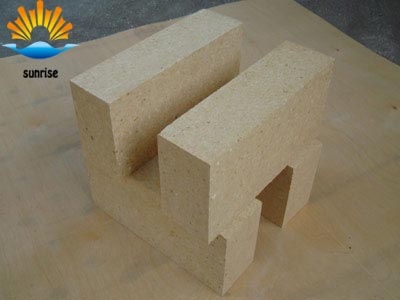
Silica has seven crystalline variants and one amorphous variant. These variants can be divided into two broad categories: the first variants are quartz, tridymite and cristobalite, which have very different crystal structures and are very slow to convert from each other; the second variant is a subspecies of the above variants. ——αβ and γ type, their structures are similar and they transform into each other faster. The raw material for making silica bricks is silica. The higher the SiO2 content of the silica raw material, the higher the refractoriness. The most harmful impurities are Al2O3, K2O, Na2O, etc., which can seriously reduce the refractoriness of refractory products. Silica brick is made of silica with SiO2 content of not less than 96%, adding mineralizer (such as iron scale, lime milk) and binder (such as molasses, sulfite pulp waste liquid), mixing, forming, drying and firing. And other processes are made.
Silica brick is mainly used in the carbonization chamber of the coke oven and the partition wall of the combustion chamber, the regenerator and sediment chamber of the steelmaking open hearth, the refractory of the soaking furnace, the glass furnace, and the firing kiln of the ceramic. And other load bearing parts. It is also used for high temperature load-bearing parts of hot blast stoves and acid flat furnace tops.